Planning for Easier and Better Project Delivery with George Hunt
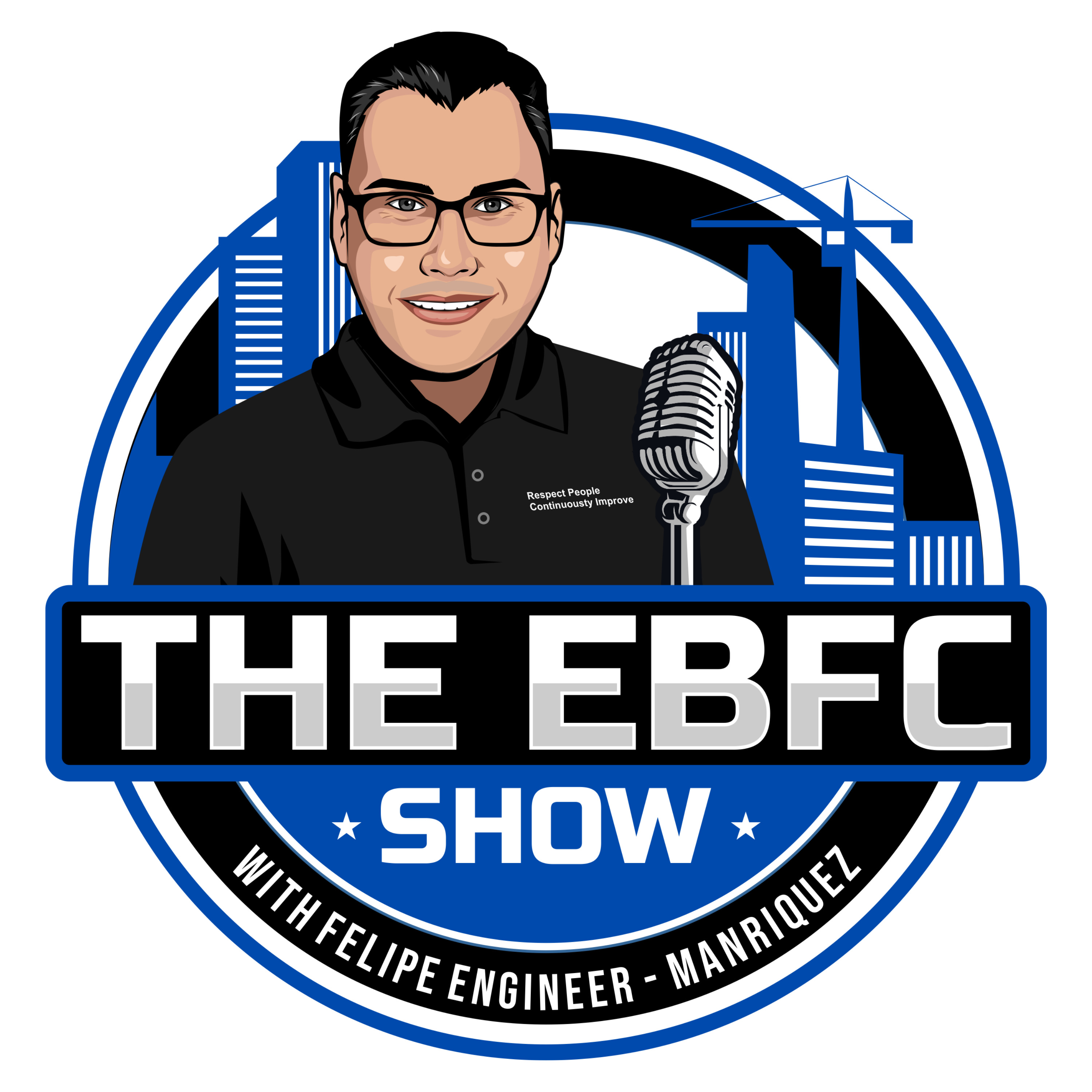
George is someone who has direct experience implementing Lean Construction on large or small projects alike. He's sharing insights about how we can make work easier, better, and faster from within our own. He directly implements Lean Construction on larg...
George is someone who has direct experience implementing Lean Construction on large or small projects alike. He's sharing insights about how we can make work easier, better, and faster from within our own. He directly implements Lean Construction on large and small projects alike. From his early days of implementing the Last Planner System as a project manager to teaching at Boston Architectural College to now serving as Corporate Lean Director at IPS, George lives for making construction work better daily. He is an excellent example of creating sustained construction company organizational improvements from the inside. George is actively serving as the Corporate Lean Director at IPS and works as a Revit Instructor at Boston Architectural College.
Connect with George via
LinkedIn at https://www.linkedin.com/in/huntg/
Connect with Felipe via
Social media at https://thefelipe.bio.link
Subscribe on YouTube to never miss new videos here: https://rb.gy/q5vaht
---
Today’s episode is sponsored by Bosch RefinemySite. It’s a cloud-based construction platform. Bosch uses Lean principles to enable your entire team, from owners to trade contractors – to plan, communicate, document, and execute in real-time. It’s the digital tool that supports the Last Planner System® process and puts it all together in one simple, collaborative ecosystem. Bosch RefinemySite empowers your team, builds trust, creates a culture of responsibility, and enhances communication. Learn more and Try for free at https://www.bosch-refinemysite.us/tryforfree
Today's episode is sponsored by the Lean Construction Institute (LCI). This non-profit organization operates as a catalyst to transform the industry through Lean project delivery using an operating system centered on a common language, fundamental principles, and basic practices. Learn more at https://www.leanconstruction.org
––––––––––––––––––––––––––––––
The EBFC Show Intro Music: California by MusicbyAden https://soundcloud.com/musicbyaden
Creative Commons — Attribution-ShareAlike 3.0 Unported — CC BY-SA 3.0
Free Download / Stream: https://bit.ly/al-california
Music promoted by Audio Library https://youtu.be/oZ3vUFdPAjI
––––––––––––––––––––––––––––––
George Hunt 0:00
Gotta make the run out to Dunks, later. Very good. Coffee,
Felipe Engineer 0:04
I love Dunkin Donuts, coffee, it's really good.
George Hunt 0:07
There's something about it that it's just it's like a drug, you mean is you have it. And it's, I mean, it's, it's really good. You just get addicted to it. It's like you can go to wherever and get like really nice cups of coffee that are all, you know, brewed and whatever. But it's like some reason you're like, I haven't had a cup of dunks in a while.
Felipe Engineer 0:25
I think it's all the sugar in the air surrounding where the coffee is made and all that, that powdered sugar just gets up into the air and then gets into the coffee canister and grounds and then boom, yeah, sugar free.
George Hunt 0:40
Yeah, exactly.
Felipe Engineer 0:43
It's got an extra something to it, though. For sure. 100.
George Hunt 0:47
Maybe a little less now? Because I don't know how many of the places actually make the donuts still in house tomorrow, just shipping them in to all the different places. But yeah,
Felipe Engineer 0:56
that's a great question. What the? Maybe when you go to dunk, so you can find out do some recon?
George Hunt 1:03
Yeah, I'll have to, I'll have to they are local. They aren't a local company. Technically,
Felipe Engineer 1:08
just one thing before we start. What made you go into
George Hunt 1:13
actually, I kind of backed into scheduling was, so I was a pm at the time. And the head of ops at the company was that was deciding on a position that they wanted to make where they wanted to combine someone who could help out and facilitate the Lean sessions and pull planning sessions and last planner on jobs. And I happen to be the person who had the most experience within the company on kind of our larger jobs. And so they can ask me, they said, hey, you know, do you want to do this? But also, we're looking for someone to start up the scheduling department internally, are you interested? And so that kind of came along with a gig, so to speak. So that's kind of how I backed myself into scheduling there was it wasn't a conscious, like, oh, I want to go into scheduling, it was kind of a, you know, I'm going to take on more of a role in the company to help facilitate and grow lean. And it's also going to be, you know, building up the scheduling department and capabilities in house. So I had the opportunity to kind of build some SOPs that encompassed everything together. So that's kind of how I ended up getting there. So there was no formal training or anything like that. I just kind of backed my way into it said, Yeah, sure, we'll do this.
Felipe Engineer 2:31
Yeah, check that out, listeners, all the people listening. Elaine was so powerfully important to George, that they said, You can do this. If you also do scheduling and start a scheduling group. I think that is the first of its kind George.
George Hunt 2:47
It could be. It could be Yeah, no, it's, I don't most people look at it. And they said, Okay, you did scheduling and lean. So it's kind of like a walking oxymoron. But, ya know, it might be the first of the kind, but that's kind of what it happened is, I mean, I had experienced just on the jobs, at least with scheduling, and a little bit of dabbling around at V six. But once that kind of happened, I said, Okay, well, I need to kind of switch gears here and really research and dive into what it takes to actually be a scheduling department and scheduler. And so yeah, I just said that, that always kind of came for me in my brain, at least secondary. But once the department got up and running, it was obviously one of the things that the first and foremost that we would handle. But yeah, always tried to get some of the lean into how we actually ran and, and scheduled and planned on our jobs anyways. So
Felipe Engineer 3:41
I think the other thing that people need to know is that you're trained as an architect, and Sam, that's like, even more like anti know, scheduling than, than anything else. I think, even more so than all the lead experience that you have and what you were doing.
George Hunt 3:57
Yeah, no, it is my my I went to college for architecture. So I ended up going through that and my I had an internship while I was at at school, and it was with a cm firm, who was looking for architects because specifically they were looking the were kind of up and coming with their VDC and BIM capabilities. And really, at the time, the only people who knew Revit were architecture students and design design people. So they were like, We need people who are going to be able to use it. And so I did a, an internship there that kind of did it for me that sealed the deal. And I was like, Okay, well, I'm not going back into architecture. I'm going to finish my degree and I'm going into cm so I went from the dark side to the dark side and then over to the dark side of scheduling.
Felipe Engineer 4:47
And then he went to The Bright Side of software. Yeah.
Sponsors 4:51
Welcome to The EBFC Show, the easier, better, for construction podcast. I'm your host Felipe Engineer Manriquez. This show is all about the business of construction. Today's episode is sponsored by Bosh RefineMySite is a cloud based construction collaboration platform that applies Lean principles to enable your entire team to plan, communicate and execute in real time. It's the digital tool that works in tandem with your last planner system process and puts it all together in one simple, collaborative ecosystem. This easy to use platform is available in English, German, Spanish, Portuguese, and French and can be used on desktops, tablet and mobile devices. According to Spencer Easton, scheduling manager at Oakland construction, refined my site in my opinion, is the best cleanest tool on the market for the last time. Here's what our users have to say. We've looked at three other digital scheduling platforms and none compared to the straightforward approach refund my site takes from milestone planning all the way down to daily tasks. This program gives every general contractor and their trade partners meaningful collaboration, accountability and KPIs. Registered today to try refine my site for free for 60 days. Today's show is also sponsored by the Lean construction Institute. LCI is working to lead the building industry and transforming its practices and culture. Its vision is to create a healthy and thriving industry that delivers outstanding project outcomes every time for everyone. Check the show notes for more information. Now, to the show.
Felipe Engineer 6:39
Welcome to the show, George Hunt, George, you and I became friends first on LinkedIn. And then hashtag IRL in real life, ladies and gentlemen. And I've had the honor of being on was it show one was show was it of your podcast?
George Hunt 6:57
It is show one? Yeah. So it was part one of show one?
Felipe Engineer 7:00
Yeah. Part one show one? Yeah,
George Hunt 7:04
I think first guest actually out of the gate two. So there was three guests on that on that, that episode. And yeah, you were first guest out of the gate. So
Felipe Engineer 7:13
we'll put a link to that show in the show notes so that you can listen to George's masterful interviewing skills of me on that show. That was a lot of fun, George and who definitely didn't plan enough time for all the conversation we had to do. So we had to have you come back on to our show. The NBFC show listeners pay attention, as you always do. George has some nuggets and some wisdom. He has a non traditional path, as you heard. But he's got a lot of things to offer. And I think you're going to learn something new. I'm expecting quite a few surprises here, George. And then no.
George Hunt 7:48
Okay. No, I will not disappoint. I will do everything I can. I'm not a person who likes to disappoint. So
Felipe Engineer 7:54
he won't disappoint. And he's already leveled up because he has one of the greatest podcast microphones that there is exactly the same one that I have.
George Hunt 8:04
Yep. Yeah, we just established that we pretty much have the same exact setup all the way down to the webcam as well. So that's good. It's
Felipe Engineer 8:11
a webcam. It's a small world. So with that, George, please go ahead and introduce yourselves and spare no details. I'll interrupt you if you go too far back into your childhood.
George Hunt 8:23
Okay, fair enough. I was gonna say so on a day in October. But no, yeah. So let's see where to start. So Happy belated
Felipe Engineer 8:31
birthday.
George Hunt 8:33
Oh, thank you. Yes. Thank you. That was that was good. So that was a nice little birthday. I celebrated the weekend on what we're out there at LCI. So it's nice to roll it into it. But yeah, so my background so as we kind of talked about, as you know, I trained as an architect went to design school, and then I came out into the CME world. And I'll the number of different positions from starting out in VDC. And then in modeling and coordination, and then kind of shifted to being out in the field for a few years as an assistant super, and then, you know, shifted into the office as an assistant PM. And then, as we were just talking about, I kind of took up the position that the company was apt to stand up the kind of internal scheduling department and also take over as lean champion within the company. And so that's kind of what I was doing for the last three or four years before I made the jump to where I am now at touch plan. So I head up our sales engineering team here, which is new within the company to is touch plants experience and a lot of growth. So you know, they've been going out and grabbing some new great talent and kind of building up the team we have here to help build a better offering for, you know, clients and customers and helping them solve the problems that they have. So I'm here now and that's kind of what I do. I get to talk to customers on a daily basis and help them solve their problems, which is a huge passion of mine. So it's working out great
Felipe Engineer 10:00
That's awesome. Thank you for sharing that. And, George, when you were an assistant superintendent, I'm curious, what was your favorite trade and tell us a story about why that trade crept its way into being special to you.
George Hunt 10:14
So I think it ended up being the electrician. And on a specific job that I was on, we were renovating one of the old mills here in New England, which in New England, we have a lot of it was an old textile mill, right on a river, very stereotypical. But the bottom, they were redoing it into some condos and apartments, and so a bunch of different buildings. And so it's pretty complex. And it was actually the first project that I had jumped on as an assistant superintendent. So out in the field, I'm trying to do the BIM coordination, and all of that, as well as being the assistant superintendent. And the electrical foreman, I think just right off the start was super friendly, and helpful. I mean, as he was participating in all the the coordination meetings, and just, you know, really nice guy, and not that everybody else wasn't, but you know, he just was extremely friendly. And then I think I remembered is on the job on a regular basis within the summer is, you know, they would end up having to scrap copper from all the cuts of the wire and things like that. And, you know, people do lots of different things with it. But what he would end up doing is they would end up going and bring it to the scrapyard getting money for it, and he would save it. And then at the end of the week for the summer, is he would buy stuff and have a barbecue for all the guys on the jobsite. And so we would end up pitching in and it was kind of what he did almost every job he was at. So all the scrap copper and things like that. The Plumbers ended up joining in and kind of taking theirs and they would kind of go and you know, turn to scrap copper and bring the money and then they'd all kind of buy stuff and so on a pretty much, you know, weekly, if not bi weekly basis, we would have a cookout on a Friday, and we'd all kind of hang out and, you know, to have a few laughs eat some food during the lunch break and then go back to work. And so, you know, just I think his the way how friendly he wasn't helpful to me, but then also just seeing how he interacted with everybody on the jobsite. I think it just it was one of those things where I was kind of like, yeah, okay, you know, there's the perception of construction workers out in the field of being rough and gruff, and everyone's yelling at each other and throwing hardhats across the room. Which does happen, but you know, if that's not how it always is it you know, it's kind of nice to know that people out there still nice and humans and can actually have civil conversations with each other.
Felipe Engineer 12:41
So yeah. Beautiful child, too.
George Hunt 12:44
Yeah, no, it was good, because we were lucky enough where there was a local butcher shop right down the road. And so they would go go to the butcher shop, get a bunch of meat and stuff for people. And so yeah, it was, it was really cool. So I think that's what ended up happening. And why I ended up will say, gravitating towards the electrician on that job, but to be honest with you is all the trades on that job. And when it came to the foreman, they were definitely top notch, some of the best that I've worked with throughout my career. So
Felipe Engineer 13:11
that's an incredible story. It's a testament to the men and women making construction happen. Like George said, there are good people out there. Definitely creating some culture, that's a very good way to create a positive and healthy culture that does honor and respect people. George, thank you for sharing that. That nugget. There's the first surprise, you've already checked that box for me. And everything else that we talked about now. It's just gonna be bonus material. Awesome. What I wanted to also ask you, in your you said, you mentioned on, on scheduling that you are self trained as a as a young assistant manager, and then PM, you're about at the pm area, in your career when you're shifting at some of those scheduling things, or where were you in your career roughly?
George Hunt 13:57
Yeah, yeah, I was reading about it that the project management level. So it was kind of a discussion of do I take this position on as kind of the next step and kind of build it up? Or do I want to stay on the project management track and kind of, you know, I ended up getting a promotion to pm, me and and kind of start running my own project. So it was that was kind of the decision where I was at.
Felipe Engineer 14:21
Okay, you chose and then you did actually get the, I see some alphabet, behind your name. So I know that you've actually trained you tell people what you earn there. And what's that? What's that about? And is it would you recommend it to other people?
George Hunt 14:36
Yeah, so the PSP certification, so it's through ace, so AC, the Association of a cost engineers. And so I would definitely recommend it to people if you're looking to do some formal training and get some credentials behind it. I mean, I think credentials aren't for everyone. And some people you know, tend to put more weight on them than others. I think When I was doing it is, like I said, I didn't really have any formal training or any sort of background where I was like, Okay, this is specifically on the scheduling and planning front. And so I kind of went through and did a bunch of research. And there was that was one of them that I came across that said, Okay, this seems like there's a good amount of people who have it from a reputable organization. And so I went through and did the test. I didn't end up doing any sort of classes beforehand. But you know, I brought up the manual and found the whole knowledge base that you needed to know that and did a little bit of studying and took the test to get the certification. So I mean, I definitely recommend it for those who are looking for different certifications to have. But I also would say that it's not in my eyes, at least, it's not something that's necessary to say that, you know, you know, scheduler can do scheduling and planning. I think it's, it's one of those things where I feel like it's kind of a toss up on whether or not people put stock into the certifications or not. So yeah, it's kind of a personal preference. But it's something that if you're into that, I would look into
Felipe Engineer 16:04
it, is that something that you'd recommend people get their employer to reimburse? Or is that something that as part of your personal professional development, that you'd recommend people take on those costs themselves?
George Hunt 16:15
So I would say try to get your employer to reimburse you on it. And you know, and from the standpoint that I think the certifications for me at least, is that's more of the client facing front facing kind of thing that you can put on the resume that when they go and put the job RFPs out and responses that they can put that on, oh, this is they're on our team, here's a bunch of the, you know, the acronyms and certifications they have. Whereas I think, you know, you can go through and learn everything there is behind the certification on your own. So to me, like, I feel like the, the knowledge and the learning that you get from the journey to get that certification is more for you. And the actual credential itself is more for the company, so to speak. So I would say try and get your company to pay for it. But, you know, if you're, if you're out there, and you're not currently at a company, and you think that it's something that would get you the next step and be able to get you that position, then, you know, maybe it's something worth investing in. But I think it's it's situational. But yeah,
Felipe Engineer 17:18
perfect answer. George, again, another nugget of wisdom for all the people, the audience here in the EBSD show, definitely we would classify as a learning community for sure. And on that note, George, I wanted to ask you some questions about learning and capability development, you've mentioned a lot of different areas, you've done some cool internships, you've worked in different roles inside the industry. What do you offer? Or what do you want to share with people about the importance of learning and capability development?
George Hunt 17:49
Yeah, I mean, I think the thing I want to share is that, you know, my journey with Lean construction is it definitely started on the surface with last planner and be like, Okay, this is a planning tool, we're doing this and planning. And I think, the more that I've got into it, and researched and heard from people in the industry, and just figuring out really what Lean and lean construction is, is, the more you start to realize that it's not, you know, the planning aspect of it, and the coordination, all that that's, I don't want to call it the surface stuff. But that's kind of the results. That's what you get out of it. And that's kind of what you're doing with it. But at the core of it, it is about learning and building our own capability, right. So the last planner, and all the cycles of learning and feedback is meant to make us better at planning, and make us better at scheduling and talking to each other. So that we can get better results on our jobs. And so that's kind of at the core of it. And I think that too often we're taking that approach that this is a tool, this is what we're looking at. And I think we're we're definitely on a trend now with a lot of us in the industry who are trying to push for that core belief that we're trying to build the capability of people. And that's what we're that we're trying to do at the start. And so I think that's part of where, you know, the the movement, I guess you can call it of folks talking about how, you know, clean the four letter word lean, is where, okay, we're not gonna talk about Lean anymore. I mean, because I think it's, it's been around enough now where people hear lean, and they go, Okay, I had some sort of an experience with it, whether it was last planner, or an executive came in and tried to push it on the whole company, and just whatever. And so there's already preconceived notions of it. And I think, at the core of it, whether we call it lean, or we call it anything else, it's a benefit to everybody to actually follow the principles behind it and actually get people to learn and get better at what they're doing because it ends with a better result. And I think, you know, right now we're doing a lot of really good work and outreach and talking and and everything else within the industry. You know, not just at LCI, but everyone who does things on their own outside, you know, this show among them is getting people to kind of realize that is really it's for everyone. So when people go and say, oh, you know, yeah, it's a manufacturing thing. It's like it's not right, you're looking at the surface level of it of its manufacturing, it's the core of it is about learning. And so you know, everyone wants to learn, everyone wants to get better. That's the whole idea behind this is we're trying to get all of us to work in a way that we're getting better all the time. So you don't have to consciously think, Okay, well, I need to take a couple hours, or it's the end of the week. Now. Now it's my time to learn, right? It's kind of is that are we're doing on a regular basis,
Felipe Engineer 20:35
or you're on your own time, at your own time, you can't learn at work, you got to learn on your own time. Exactly. Which I totally disagree with.
George Hunt 20:45
No, absolutely. I mean, we need to be learning while we're at work, it's, you know, it, as scary as it might sound for some employers to think that, you know, people are going to be quote, unquote, experimenting, or trying new things at work to learn more, it benefits everybody, you mean, as it gets the people who are doing the work better at it, it, you know, it's going to benefit our employers, because they're going to get a better product at the end of the day, whether it's, they're working more efficiently, so they spend less hours on something, or just the quality of the job comes out better, whatever it might be, they get a better quality product at the end of the day. And then same with the owners and designers and everyone else who's there to is that, you know, you're gonna get better quality things are gonna get done on time, they're gonna get done the way that we're all kind of intending it to be. And I just don't think that, you know, the industry as a whole spends enough time on that piece of it is understanding the lien isn't just a four letter word is not a tool. It's it's, you know, it's kind of it's a way of thinking. And I think if we we kind of focus on thinking about developing ourselves while we're doing our work is I think that's kind of the key here. And so, I know it's been a project, if you will, of mind is that's what I'm trying to spread and get people to understand a little bit more. Is that what the core of it is, and whether you're doing less planner, or you're trying to use Scrum, or you're trying to do anything, is that's kind of at the core of what we're doing here. Right. And so, call it what you will use whatever tools you want to, if at the core of it, like you're getting better at what you're doing, and we're getting better as a whole, then, you know, as far as I'm concerned, we're, we're at least making progress there.
Felipe Engineer 22:30
I completely agree. And I absolutely love the fact that you mentioned my favorite word, Scrum. Thank you for that, George. That's a gift. Very Christian. Yeah.
George Hunt 22:38
Absolutely. And I'm actually I'm taking your scrum master course here this week. So I'm a member and signed up. So I'm, I'm on board there. I love it. I'm gonna, I'm hoping to grab some great nuggets out of that and be able to apply it to some who don't know, Scrum. So your is on there, too.
Felipe Engineer 22:59
Yeah. And I'm gonna come back to you for for feedback on the course afterwards, because I think your perspective is so, so diverse, it's going to be really cool to hear what you think about it. And I want to just unpack a couple of things and what you said there, a lot of people do have a bias against the word lien. Thank you media in the United States for making liens. Such a nasty word that George absolutely is correct. And referring to it as the four letter word inside of large corporations and businesses and construction and even design firms. It is seen as a very negative thing, because people tend to associate lean with either the very surface level, just eliminating waste, which to a lot of people without understanding what that even entails looks like extra work. If I have to get rid of things, that just looks like extra work. But that's a very surface level understanding though, the more dark the darker side, I would say that the media portrays lean. And we've seen a lot of things with the supply chain recently, messages against a just in time, type of supply chain without any understanding of supermarket concepts or inventory buffers. People that just trying to make headlines and splash that try to try to get us to believe that Lean is an acronym that stands for less employees are needed, or doing more with less, which is absolutely not the case. John craft SEC and the team that that coined the phrase way back in the day, they didn't want to call it the Toyota Production System. Just didn't want to call it that. But it was a philosophy that at the time when they were studying, it was very hard to put some language on and then later in the early 2000s When people got together at Snowbird and created the Agile Manifesto, they also said because lean was already negatively perceived in the media that they didn't want to call it lean, even though the roots of the Agile Manifesto are deeply embedded in Lean philosophy, concepts and methodologies. So I think it's just fascinating that we, we don't like it, but it's the best closest word there is. And I guess we didn't want to just call it learning. Because our adaptation, so we couldn't be there, George, we couldn't go back in time, you and I, and tell people like, probably no matter what they called it, there would be people being negative towards it, because it looks like extra work from the onset, if you're looking outside in, or if an executive forces it down your throat. I've seen a couple of recent articles on the Lean builder, Jesse Hernandez just had a post. And he said, his introduction to lean was some executive saying here, you have to do this extra stuff now. And that was his foray in which luckily for him, that extra stuff actually built some more capacity for him. And he got interested in curious and more, but how many people do we know George, that they don't have that luck of what they get forced the wickets forced upon them? Actually does benefit them? I'm sure you've heard some last planner story nightmares. And then I want to hear more about your take on last plan or two. So I'm going to ask you like seven questions, and you just pick which one you want to answer are all fascinating. Yeah. So I'll just hit them all. Because you said that, you know, just to sum, when you first are looking at last winter system, it doesn't appear to just be good conversation. It looks like a whole bunch of extra stuff, doesn't it?
George Hunt 26:38
Yeah, absolutely. It does. And I think that's, you know, listen is, I mean, are there the jobs where they don't really do any planning at all? So technically speaking, it would be extra work. Sure. Right. But like, Listen, if you're not doing any planning, then you should probably be doing planning anyway. So yes, let's add this on top of it. You need to plan, right? We'll put that. But um, but yeah, is I think people look at it as extra work because so much in construction, the, the culture we've built is, well, we're not going to talk about this, you're just going to tell me what to do. And I'm going to go do it. So when we come to a room, and we come and sit everyone down, say okay, we're actually going to have a conversation about what should actually be happening here and what you want to be doing. Because it just makes sense to ask the person who's the expert on it. What do you actually want to do with this? You know, if people look at it as extra, and because they're not used to it, and they're not practiced in it. And so it does end up being that initial poll, where you're trying to drag people along to say, Listen, this is an extra, let's just Just come with me here. Come on, come on the journey with me, and just let you know, just look at it, let be open to it. And let's do it. And once it starts to work, they're like, Okay, and they start to see that, well, now that we're doing this and having these planning sessions on a weekly basis, and we're having, you know, whether you're doing the sticky notes, or using something like touch planning, going digital is what, you know, just having a more collaborative planning environment is people start going, Okay, well, well, I don't need to spend the two hours a week, three hours a week I used to spend on Sundays while I was watching the Patriots game to do my schedule for the week. It's like, Yeah, I know, we all just did it. In the regular meeting that we were doing every single week, like, okay, so it's not extra, it's actually less than what I was doing before. And I have people helping me. So you mean, I'm spending less time to get more out of it? It's like, exactly right. And so, you know, we're so visual, and we're so tactile, and construction all the time that we really need to get just let's see an experience at first to say, Okay, you're right, that works. Okay, great. Now, let me see a little bit more, it's, let me dip the toe in the water, feel that it's actually warm. And then let me start to go in the full way. And so I've had plenty of experiences with that, that people, I've had to sit them down and kind of say, okay, you know, what's the reasoning here and really get down into the Why don't you want to do this kind of conversation. And then just get them to trust me enough to say, Listen, I'll be there to help along the way. I'll facilitate it. You know what I mean? I get it that you don't know how to do this yet. So let's work along the way here. But just trust me that there's going to come a point where it's going to work, we're going to see some sort of benefit, and then you're going to say, Okay, you're right. I don't know why I did it any other way. And so there's a great example of that, where I had a team and a superintendent who pretty much said that exactly that like I don't want to do this. This is stupid, right is I've had at a different place as we tried to do pool planning before it didn't frickin work. Right is I don't want to sit down here and all this time with the foreman and bring them in, they need to be out there in the field. Right and so that energy kind of radiated for the whole team. And so the the foreman was saying the same thing like Okay, great. So I sat him down and I said, Listen, we were we're going to do this right is that, you know, the project exact says, Hey, we really want to push and do this. It's gonna be better for the client. Right? Let's let me what what is it that you don't want to do? Right? What what is it that doesn't work and his whole thing was that he's like, Well listen, I'm the superintendent, I'm supposed to be interacting with jobs. You mean? So it's my plan, I want to be going out there. And people are supposed to be following what I do. And this man, I'm like, Okay, well, listen, it can still be your plan, right? Like, listen, you you, you built the master schedule, and you have the overall vision on it. So when we're having these planning sessions, have that for a guide, while you're sitting there looking at it. And so if something starts to go in, the plan starts to change from what you had big picture, stop and say, Hey, guys, you know, we have a milestone that we have to meet here. We still have to meet this milestone, what are we going to do. And so that was kind of the in between that I was able to get him to actually sit down in the meeting. Fast forward to the end of that job. And it was about a 10 and a half month job, I think it was and it was a lab fit out, we did for one of the local
research facilities for the for one of the hospitals. He basically was like, I'm not doing this any other way. And he actually got up into that monthly superintendents meeting, and told the team, you know, this was when we were rolling out, trying to do much more of a robust Weekly Work Plan, process. And you know, we were at the time rolling out touch plan kind of company wide. As he said, You guys, this works, right is like, I didn't like it at the beginning. I didn't think it was gonna work. But he's like, it takes time out of my days. He's like, I don't have to answer my phone every 10 minutes. Because the formatter fine talking to each other. And then at the end of the day, anyways, when we do our standup, he's like, all that comes out in the wash, and we figure it out. He's like, it works. He's like, believe me, he's like, I remember when I had the conversation originally with our COO, and I was like, There's no way I'm doing this stuff. He's like an A, George came, and he's like, I'm not doing this stuff, you know, let's go. He's like, now he's like, I'm not doing it any other way. And the next job that we won, because we were so successful on that one, we want a kind of a copycat of that, on an upper floor in the building, we said, we're bringing all the same foremen, we're bringing the same job, the same crew, let's just do it again. And we did it. And it was just as successful as the last one. And so that was kind of, I always like to talk about as that's kind of one of the crowning jewels, so to speak of, I can say listen to this was a guy who was way over here who didn't want to do it at all. And by the end of it, he's like, I'm not doing it any other way. Just because I think it, it went so well. And he was able to see that it's not extra, it was actually, you know, it's just new stuff that when you get used to it, it actually takes time away from what you would usually have to spend on it. Yeah,
Felipe Engineer 32:52
yes, absolutely. George Irwin. Listening, George has just given you another perfect nugget, let me just unpack it a hair more so that people think if you missed the magic and what he just did, and what he described as that he had a skeptic, and everyone who knows me knows, I love skeptics. Because they are thinking about risk and what can go wrong, or they have experiences and they know stuff has gone wrong. And George slowed down and had a one on one conversation with the superintendent to see what didn't work. And then they were able in the safe way to talk about it without losing any face in front of the other people or being diminished in any way that is powerful to give people the space to tell you why it can't work and then to show not tell, but to show what the process is going to be. And that where are they in the process? Right? Because the superintendent did not get eliminated from the equation. No, right? And last punter system, you still need that superintendent to be that the center, the center spoke of the wheel of all the value creators, for sure they're coordinating, it's more than just the contractual thing. If you have a general contractor on board with trades, information does have to flow. And there is a benefit to having a central person on there leading the charge. So superintendents, if you're out there, and I know that a lot of the superintendents listen to the show George they use last month or system in every single project. If you're out there and you're thinking like well might be too hard. I mean, now more than ever, there are so many free resources, good resources that you can see on what good laughs planner system look like what it looks like. I recommend Joe and key ons book, The Lean builder to see another yet another example. Right, George, you've read that book?
George Hunt 34:47
Yeah, no, absolutely. I think that's a great way to kind of ease your way into it and stick your toe in like, like I was saying before, stick your toe in a little bit. Change things gradually over time that I think are less, less scary and then Work your way up. But yeah, it's a the way they lay that out I think is a great way to start to get into it.
Felipe Engineer 35:06
Absolutely. And if you if you want to dip your toe like super toe dip, like don't even get your, the base of your foot wet, no heel in the water, you can always just expose your milestones out with the superintendent and have dialogue with the trades. On that floater high level, there's something magical George about taking it outside of bar charts and just exposing it either on a on a whiteboard, or his diamonds and software in a program where people can move the stuff around easily without, you know, a lot of rigor Murrow the easier it is for people to expose their thinking and check that sequence. I think it really anchors people. If I can move something around, we had a job where an electrician brought to us in our master schedule that we did, we forgot that there was a very critical transformer to the power generation yard that was going to cut the whole building loose for permanent power that had to come out of a different sequence just because of a door. I mean, no one had thought about that. No one had thought like, oh, this door is going to become an issue. And so I mean, that if we had not had that milestone conversation, we would have missed that. And it would have cost money that unfortunately, we would have had to pay for. So right that electrician saved that saved our bacon. And also got us to move up earlier. Permanent power, which is nice. It's very nice to have permanent power in a building. So nice and luxury.
George Hunt 36:34
Yeah, no, absolutely. He kind of you kind of need that for things.
Felipe Engineer 36:39
Yeah, keep the lights on.
George Hunt 36:41
Yeah, I will say the one more thing I do want to add with the last planner. And I think it goes to it was a conversation I was having with I know, you know, how may comer. And when we were kind of preparing for the course we taught at LCI, which was an intro to tech planning, you know, one of the four hour courses there workshops, but we were talking about, he was incorporating in kind of why Lean and lean ideals have kind of caught on to other industries and what they're doing differently than us. And one of the biggest things that we were talking about is that whether it's manufacturing, or whether it's healthcare, and their healthcare operations, or any of the other industries that you look at, they engage the frontline people to actually improve the system that they're working in, right in construction, unless you're doing last planter, right is there's no way for the men and women who are in the frontlines actually doing the work to come and give feedback to improve the process that we're doing. And so and like, that's where I think such a big opportunity is for us is just getting the feedback and engaging them and saying, hey, what can we do to make this better, right, and there's the whole horizon of different things, what that looks like, whether it's last planter or whether the trays themselves are doing five s out on the job site on there. You know, I mean, something along those lines, there's so many things they can do. But we just don't engage the workers and the people actually doing the work. And when you kind of step back and look at it and think it's like that is the only thing that makes sense. The economy is they're the ones who are actually doing the work, why wouldn't they know how to improve it better. And they're also probably going to give you an improvement, that isn't going to cost a huge amount of money to implement, because they're not going to want to change a whole bunch of stuff they're doing, but they're going to want to do something that's going to make it better for them to do the work. So like, they're gonna say, hey, well, maybe if we went instead, we organized our job card a little bit differently here, great, it makes it easier for them, you know, what costs you 1020 bucks to get some dividers in different boxes for the car. There you go. You know, and so there's it, I think that's one of the things that we do a terrible job of is engaging the men and women who are actually doing the work. And we have such of this top down mentality that all the innovation and all the ideas are going to come from the people in the leadership roles and kind of trickle down. And if we just look at the industries who have been successful in implementing Lean In this kind of learning, ideal, that's what they do is one of the big things is they engage the people who are actually doing the work.
Felipe Engineer 39:18
Absolutely. A companies like Toyota, where they create an environment where employees are giving two plus improvement ideas a day. I mean, could you imagine how cool if I was on a job site and all if I was 1000 person job site, and everybody gave two ideas every day, I'd have 2000 ideas that day. How would I even deal with that, like construction? That seems so foreign because you imagine that that problem, George?
George Hunt 39:45
No. I know. I mean, even it's still, the idea of having that much is still kind of foreign to me too, because I still, I haven't had the chance yet to go on an actual tour of a Toyota plant or anything like that, but I'd love to because I want to see what that looks like. And I think it's, you know, we also have this idea of an improvement as, hey, I'm going to change something completely where that might not be the improvement. It might just be a, hey, we've moved this box from here to here, because it's a shorter reach for my hand. Right? It's something you know, to Paul Akers of the two second lean. It's something that quick, but that's an improvement. Right? So that's one of the things that we put in for the day. And that's, that's the other thing is that we, we have this perception that the improvements have to be these huge astronomical things, and they don't, there's just it's something that that improves anything, anything at all, you know, change it does is it better than it was before. Great. That's an improvement. I want to say that
Felipe Engineer 40:42
empowering the people first, like when you go visit toilet, or you read these stories and these incredible numbers, or like even Paul Akers, and what he's got going in his shop at FastCap, with all the improvements, all the foundation that that happens on is creating an environment where you a ask people for their ideas, most of the time, I've heard people say, Well, no one's ever asked me. We were on a job, or I was on a solar job earlier this year. And we were just looking at some inspection thing. And I was being my usual self asking with curiosity, and just understand, like, what's going on? And the people commented to me like this, this guy is 22 years, a laborer in construction. And he said, at 22 years, I was the first person for management to ask him a question. And I thought, wow, it's like, we're like, I just opened a time capsule and stepped into construction. 1950 something? Yep. So like, if you're on a job listening to the show, go ahead and hit pause, and go get curious about something in the field. And ask people questions, not to show like your smarty pants, but with actual curiosity, and hear from them, you know, why they do the things a certain way how things are organized. And then as people talk a lot, expose their thinking, and innovation will emerge. And encourage those people, if you're in a management position, encourage your people to go ahead and make little improvements to benefit them, benefit them first. That's why it's called the NBFC show, George, the first thing we want to do is make it easier for our people.
George Hunt 42:24
Absolutely. And if it's easier for them, that means that they're going to be doing better work on top of it. So from a management perspective, it's a win, win, win win, it's win win for everyone, you're gonna get better and more happy people doing the work. They're going to put out better quality stuff. It's going to be faster. It's going to be quicker. Great. Right? There's where do you go wrong on that? Sounds right. Yeah.
Felipe Engineer 42:45
I was like, people that don't know. Like, George and I have hung out past midnight. We were at LCI, which is my typical, that's my typical jam, where I go to hang out with cool people like George. And we were we were chatting over a couple of adult beverages at you know, whatever. The third bar, I think we went to
George Hunt 43:09
maybe, whatever that one was, it might have been the Irish bar. I don't know. Yeah, it's
Felipe Engineer 43:13
a good there's always an Irish Pub in every town. Thank you, Ireland for exporting. Just good culture making, you know, locations for us worldwide. They're exactly every major city. George, there is an Irish Pub.
George Hunt 43:25
Yeah. And I'm up in Boston, which means there's probably the only place that has more Irish pubs per capita is Ireland itself is probably the way that it is. But
Felipe Engineer 43:35
that's probably true. I remember somebody, somebody from Ireland, had a friend that went to go visit Dublin. And they they called their friend to didn't even live in Ireland anymore. And they said, Hey, I'm in Dublin. What pubs should I go to? And they said, Okay, you get your hotel, and they're like, yes, it's like, go outside, turn left. First pub you walk into is going to be perfect. Ever, like, how did you know there's a pub there? It's Dublin.
George Hunt 44:03
Yeah, there's gonna be one there. It's like we're just talking about Dunkin Donuts. It's like Dunkin Donuts here in New England. It's like you turn left, there's gonna be a Dunkin Donuts. It's pubs an island.
Felipe Engineer 44:12
Absolutely, absolutely. And so I wanted to also ask you, George, you know, let's piggyback on this, this capability development. Is there ever, from your perspective, a time where improving your work wouldn't have benefits for you? Because some people actually come that their work and especially in subject matter experts, there could be a tendency towards thinking that you've, you're it like, you're at the top of the pyramid, top of the mountain. When When does it end? George?
George Hunt 44:46
I don't think it does. Me and I think it's, you know, I think when we get complacent it's when you know, if you want to call it a competition or whatever else catches up to us, it's, you know, And again, it doesn't need mean that we we stop, and we have to keep doing these monumental innovations. But you know, we it, I don't think it stops and looking at what we're doing, and understanding what's going to make it better. And you know, if you want to call them experiments, if you want to call them tweaks, whatever you want to refer to him as but take a look at what you're doing and saying, Okay, well, what happens if I changed this piece of my process or the way that I do it? And change it and see what happens? Maybe it does go worse. And then you go back through and say, Okay, well, that didn't work. But that's valuable, right? That's valuable to know that, well, that doesn't help it. But what's the other options and just kind of keep going through. And I think that we do kind of get complacent. Sometimes we're like, oh, we're at the top of the world here. Why do I need to keep pushing? Why do I need to keep getting better, but it's through that, you know, continually trying to get better at things that we bring everything forward? I mean, is I think if we stopped and said, Hey, we built an airplane, right? It's like, there's literally a way that humans can fly in the air. What else do we need to do now? You mean, is we we would stop there, right? And now look at us all these years later of what airplanes and flying can do. So. You know, I just I don't think that there's ever a time where we need to stop. I mean, I think probably on a personal level, there's, there's times where people will feel that like, okay, you know, maybe they're burnt out, or maybe they don't want to push any farther and, and so be it. And there's that whole personal aspect of it too. But I just think we can't, we can't get complacent what we're doing, because I think the second we get complacent is when problems are gonna start to happen. And we stop moving forward, kind of as a society with everything that we're doing. So yeah, perfect. And my sort of answer on that. Yeah,
Felipe Engineer 46:49
that was a longer answer. But I think it's a it's a good point, like, you know, people that come on to the show, and share their experiences. We've got people from across the supply chain. And now, you know, George, I think you're you might be you're in the top five of technology companies that have come on the show, and shared your experiences like people, competitors to be sharing competition is actually good. There is a level of healthy competition. I want to go back to, to one of the things Dr. Deming said Dr. Deming has been William Edwards Deming, for those who don't know who I'm talking about, was an amazing pioneer in quality and also foundationally set a lot of the things that we now call lean, that even people in Japan learned after World War Two was through a lot of the work that he had done here in the United States and abroad. And he was he was epically larger than life, even abroad, more so than in the US. But he'd had a fantastic career. But one of the things I remember there was a talk that he was giving those, I was lucky enough to watch a recording of it. And it was nothing but executives, there's probably over 300 executives in the audience, nothing but CEOs, CFOs, CEOs, executive vice presidents, this is the talk that he was giving in one of his seminars. And he was talking about that learning and capability development, and then this idea of complacency, the very thing you're talking about. And one of the executives was like very skeptical, raise their hand and said, So if one of my people in my company and think they were like a manufacturing company in the United States, if one of my people wants to learn about biology, am I supposed to encourage that? Like, they wanted him to say no, it has nothing to do with what you're doing? And his answer was absolutely, yes, you absolutely encourage your people to learn anything. At any time. He's like, You cannot predict what they learn how it will benefit them. And you as a result of them, improving themselves to learning something new said you have no idea. And I remember what Jeff Sutherland said when he was studying, you know how great teams work and looking at how to make things better. And it was actually his study of cellular biology, where you learned how complex systems work. And people working on projects together form a complex system. And you've got to have a feedback loops, and you've got to have communication pathways. And you have to have ways to see what's happening. And there. There are different ways to create that environment is one of the things that scrum does and so a lot of like, why Scrum works. So dasht current good. And why last planner system works so well because it's borrowed a lot from Scrum. By the way people I've heard I think people have heard me say that before. This is your first show. Our system has borrowed heavily from Scrum. You have to just be open. You might learn something in a completely different domain. And that benefits you. And that's, that's available to all of us. And competition is good. If you talk to your competitors about what they're doing, you might get inspired. You shouldn't compare yourself to beat yourself up. That's not positive for you. But you can absolutely be inspired to see there. There are other ways. And you can get better every day, as George has so beautifully pointed out to us. Thank you, George for that. Absolutely. Yeah, I want to give, I want to give you another since you're dropping all these these nuggets, George, as you've transitioned in your career, a bit and you've changed and occupied different roles. Is there anything that surprised you? Like, what is surprised you Mr. Hunt, working at a software company and construction?
George Hunt 50:53
That I mean, I think that the problems that I was facing on a regular basis, do not just live within the company I was at. And yes, so those so those who go to LCI know that right is there's presentations and things and you talk with other like minded people, and you realize that you're not alone, but I'm talking even now, more so on a global scale, excuse me is, you know, I've had a chance to talk to companies and customers all over the world. And just to hear them talking about what they're going through, it's like, so you're in Australia, and you're doing construction that's completely different than what I'm doing. And completely different trades and different training and all that. And yet, the problem is still exactly the same, it still comes down to the fact that people still aren't communicating very well, or you mean or something like that. It's just like, wow, okay. So I think it's just the surprising thing to me. And not that I never had the idea that, you know, our problems were larger than ourselves, but just the view that I get to have in this position, where I'm talking to so many people from so many different walks of life in so many different areas of the world, that it really kind of brings everything in full perspective together to say like, you know, when we talk about learning and improving it, from an industry perspective, it really is the entire industry, it's not just, we're doing it just for the industry in the US, or, you know, over in Europe, they're doing things and just improving the construction industry in Europe is, especially now with the internet and all the conferences and things we have is that knowledge needs to get shared, because it's the same problems we have all over the world. You mean, whether it's labor, whether it's your materials, and supply chains, and all these things that keep coming up, you know, with safety, and everything else that people look at, it's the same problems across the world, right is every company goes through with it. And there's the companies who will call the superstars who are very good at certain things, but they're still, you know, the reason why they're up there and very good at what they're at is because they look at everything else in the industry and learn from it. And so, yeah, I mean, that's, I think, been the biggest eye opening thing to me, it's just that the realization that I think that I had the idea in my head anyways, but the kind of confirmation of these problems are systematic, and they go out across the world to everywhere that we're doing construction. And it's not just the US, and it's not just Europe, or South America, or wherever we're talking about, is they are all over the place. Because we're all still people. And we all still do the same stuff. Me mean, and so the work and the improvements that we're doing now, you know, in our own silos, if you will, on our projects, is sharing that as much as we can, is going to help everybody. Because just like I said, is a goes and it's prevalent across the entire world with how people do construction.
Felipe Engineer 54:00
Yeah, yes, absolutely, is that I was I had the same like, epiphany, as I did some work and in Ireland, and then I've had some connections in different parts of the world and people you know, Malaysia, Singapore, Turkey, Australia, you know, even more non English speaking, I was shocked to hear exactly what you said, George, same exact problems. It doesn't matter the type of trade, the sophistication level, they're just some common, I would say like there's some archetypal problems that are just so prevalent, like the communication aspect. I remember an executive telling me that we're talking about some challenges on a job, a very large job. And he said, I know what you're going to say. And I said what he's like, it's a communication problem. It always is. I said, Well, if it always is, and you've been doing this for 30 years, don't you have like some things that you but we can try or that we can take action on to, to mitigate this because we've been on projects that are successful. And we've ran projects that aren't. What, what's the difference than just getting people to not just throw their hands up and say, well, it's this thing and then blame something or someone. But to actually do like you're suggesting, share those improvements. We don't have to reinvent the wheel. We could just get better wheels and make them faster. Maybe like you said, George, we don't need wheels at all. We just fly.
George Hunt 55:32
Yeah. Yeah, absolutely. I think so. You know, and I think it's actually I think it was Deming, who said, the, you know, when we're looking for problems, if, if we're going to blame the people instead of the system that they're working in, and you think that is the people's fault and not the system? Take another look, because it's not the people, it's the system. So you know, the way that we work, and the way that we do things is that's the always the problem is not the people, the people are just doing what the system is designed to do. They're working within the system. So if we can change the way that we work, and the way that we're thinking and having a better environment for people, I think it's that's what we're striving for. Right? Right. Yeah. Ultimately.
Felipe Engineer 56:13
Awesome. George, you get the last word. And then I'm shutting this thing down.
George Hunt 56:18
Perfect. Last word. Well, I mean, I think your last
Felipe Engineer 56:21
phrase, you could get the last. You get the last paragraph George.
George Hunt 56:25
Oh, boy, there we go. You know, I think just to close it out for me is I think, you know, the work that everyone's doing out there right now I think keep up with it. Keep sharing, keep telling people about what you're doing, whether it's at LCI, whether it's at idlc things I know, there's so many things now throughout the world that are doing the same kinds of things that LCI is doing here in the US and the United States. So keep going to these, if you're curious, go to them to learn more. And just, you know, don't stop, I think is really the thing is just don't stop trying to get better at what you're doing on a daily basis. Because, well, at first, it might seem that it's a little bit of an uphill battle to kind of work in and all hideaway and prove something do we need to get better at it is the more you're practiced at continually looking at your work and trying to improve it, the better you get, and the less of a burden, it seems like. And so it's kind of getting over that initial hurdle and kind of ripping off the mandate, so to speak. So that's what I'd say and leave people with is keep going keep trying to improve. And if you're curious about something, is reach out and ask people, because that's the only way we learn. So
Felipe Engineer 57:36
George, value has been delivered. Have a fantastic rest of your week. And thank you for inspiring so many more people to share. Take that risk of learning. It's only going to be fun. Let's go do it.
George Hunt 57:49
Absolutely. Absolutely fun. That's the key Joe. Thanks so much.
Felipe Engineer 57:54
Very special thanks to my guest. I'm Felipe Engineer Manriquez. The EBFC Show is created by Felipe and produced by passion to build easier and better. Thanks for listening. Stay safe everybody. Let's go build!