Lean Construction Pioneer Iris Tommelein
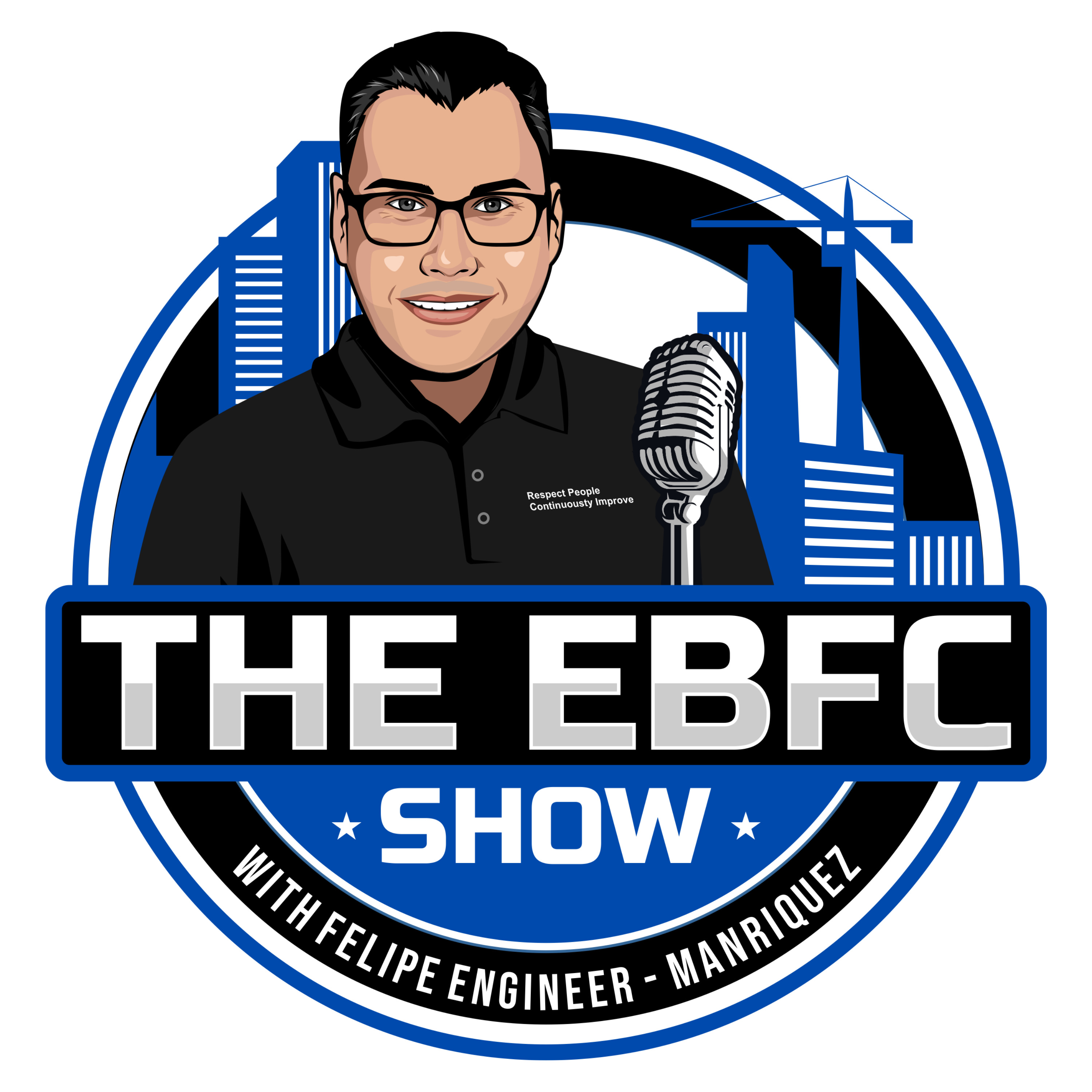
Iris D. Tommelein is a Professor of Engineering and Project Management in the Civil and Envir. Engrg. Dept. at UC Berkeley. She focuses on developing theory and principles of project-based production management for the architecture-engineering-constructi...
Iris D. Tommelein is a Professor of Engineering and Project Management in the Civil and Envir. Engrg. Dept. at UC Berkeley. She focuses on developing theory and principles of project-based production management for the architecture-engineering-construction industry, what is termed 'lean construction.' She is an expert on construction site logistics, layout, materials- and supply-chain management.
Professor Tommelein directs the Project Production Systems Laboratory (P2SL - p2sl.berkeley.edu), a research institute dedicated to developing and deploying knowledge and tools for project management as well as a learning lab for the Northern California construction industry. She is active in the International Group for Lean Construction and until recently served on the Board of Directors of the Lean Construction Institute (LCI).
LCI recognized her with the Lean Pioneer Award 2015 - The award recognizes an individual (or organization) who has moved the design and construction industry forward in embracing and implementing Lean tools and techniques on capital projects (www.leanconstruction.org/news/95/36/LCI-Recognizes-Iris-Tommelein-with-Prestigious-Pioneer-Award/ ).
Prof. Tommelein received the 2014 Peurifoy Construction Research Award from the American Society of Civil Engineers (ASCE) (faculty.ce.berkeley.edu/tommelein/papers/Peurifoy.pdf ). She also received the 2002 Walter L. Huber Civil Engineering Prize "for her research on civil engineering computing for managing project-based production systems in the engineering-architecture-construction industry."
Professor Tommelein served on the ExCom of ASCE's Technical Council on Computing and Information Technology (TCCIT) and as a member of the Research Council of the Construction Institute.
Connect with Iris Tommelein via
LinkedIn at https://www.linkedin.com/in/tommelein/
Podcast Referenced Takt Case Study: https://iglc.net/Papers/Details/902
Connect with Felipe via
Social media at https://thefelipe.bio.link
Subscribe on YouTube to never miss new videos here: https://rb.gy/q5vaht
---
Today’s episode is sponsored by Bosch RefinemySite. It’s a cloud-based construction platform. Bosch uses Lean principles to enable your entire team, from owners to trade contractors – to plan, communicate, document, and execute in real-time. It’s the digital tool that supports the Last Planner System® process and puts it all together in one simple, collaborative ecosystem. Bosch RefinemySite empowers your team, builds trust, creates a culture of responsibility, and enhances communication. Learn more and Try for free at https://www.bosch-refinemysite.us/tryforfree
Today's episode is sponsored by the Lean Construction Institute (LCI). This non-profit organization operates as a catalyst to transform the industry through Lean project delivery using an operating system centered on a common language, fundamental principles, and basic practices. Learn more at https://www.leanconstruction.org
––––––––––––––––––––––––––––––
The EBFC Show Intro Music: California by MusicbyAden https://soundcloud.com/musicbyaden
Creative Commons — Attribution-ShareAlike 3.0 Unported — CC BY-SA 3.0
Free Download / Stream: https://bit.ly/al-california
Music promoted by Audio Library https://youtu.be/oZ3vUFdPAjI
––––––––––––––––––––––––––––––
Felipe Engineer 0:00
When I first started getting into lean construction, and looking more into what this is, and where it came from all roads led back to Berkeley, where you are
Iris 0:12
University of California, Berkeley
Felipe Engineer 0:13
University of California, Berkeley, Go Bears. So, so many people that I've bumped into, over my time in construction I've been two decades in have either benefited directly from your tutelage or your education training with you or been inspired by papers that you've helped to create, or through your work with P2SL or IGLC, or the Lean Construction Institute, just so many places, you're just such a big influence. And I've recently got onto this whole path on newer and better ways to schedule work such as Scrum, Takt, and of course, Last Planner System where a lot of us first get our feet wet. When we start diving into lean. What do you have to say for yourself for all these people, you're inspiring Iris.
Iris 1:04
It's been a fortunate, fortunate to work with everyone. It's nice to work with people who are eager to learn and open to new ideas.
Felipe Engineer 1:12
Welcome to The EBFC Whow, the easier, better for construction podcast. I'm your host Felipe Engineer Manriquez. This show is all about the business of construction.
Sponsors 1:16
Today's episode is sponsored by Bosch refined my site is a cloud based construction collaboration platform that applies Lean principles to enable your entire team to plan, communicate and execute in real time. It's the digital tool that works in tandem with your last planner system process and puts it all together in one simple, collaborative ecosystem. This easy to use platform is available in English, German, Spanish, Portuguese, and French and can be used on desktops, tablet and mobile devices. According to Spencer Easton, scheduling manager at Oakland construction, refined my site in my opinion, is the best cleanest tool on the market for the last time. Here's what our users have to say. We've looked at three other digital scheduling platforms and none compare to the straightforward approach refined my site takes from milestone planning all the way down to daily tasks. This program gives every general contractor and their trade partners meaningful collaboration, accountability and KPIs. Registered today to try refine my site for free for 60 days. Today's show is also sponsored by the Lean construction Institute. LCI is working to lead the building industry and transforming its practices and culture. Its vision is to create a healthy and thriving industry that delivers outstanding project outcomes every time for everyone. Check the show notes for more information. Now to the show. Welcome to the show. Dr. Iris Tomlin Iris, thank you so much for coming onto the show, and sharing with the world as you've impacted so many students that I've come across including in Germany, in Sweden, South America, Finland, what countries Am I missing? California, California could almost be a country could it not? Maybe very, it's part of the United States. So please tell everybody tell the good people the internet how you got started with becoming a doctor and a major influencer in the construction movement worldwide.
Iris 4:50
Well, it's been a while I don't quite have all the gray hair to show for it. But um, I've been at it a little longer than the two decades you've been in It's more than three and a half decades, I guess that I've been in the industry. I was born and raised in Belgium and have a five year civil engineer architect degree from the Free University in Brussels. I had the opportunity at the end of my fourth year to do an internship for a construction company. And I ended up working for the whites company in the morning, Iowa, I had an absolutely terrific project manager who would take you know, the various students who were there, including me along to project sites, and it really opened my eyes to what it means to run a good project. So when I finished my degree in Belgium, I was fortunate enough to get a scholarship to study for a master's degree in the United States. I ended up at Stanford and earned a master's in construction engineering and management. And while they're one of the faculty Ray Levet, had just returned from a sabbatical, in Silicon Valley, learning about artificial intelligence, and so he twisted my arm, to study how we might be using artificial intelligence and apply it to problems in the domain of construction. This is 1985. So it's, it's quite a few years ago, for as popular as artificial intelligence is today. We've, you know, we have we started long time ago, but the technology wasn't quite as fast and as, as powerful, of course, as it is today. So it's been very exciting to see how our capabilities have been changing over time. But Ray convinced me to work on the problem of site layout planning, looking at how construction managers layout temporary facilities on construction site, it is a very gnarly problem, both from an academic standpoint, as well as from a practical standpoint. So he sent me out to the Gemba to go to a couple of construction sites and talk to project managers and superintendents to find out how they were doing site layout. He also sent me to a conference on artificial intelligence in Los Angeles. And on the plane, I met some people who were very instrumental in working in artificial intelligence at Stanford. And then I met one of the faculty, Barbara Hayes Roth at the conference. And she invited me when we got back to Stanford to come talk to her about how we might use the rule based system that she was working on the blackboard system she was working on at the time, and try it out for the site layout problem. So it was a very, very interesting time, a very exciting time. And the time of the first Macintosh computers with 512k of memory, the glory days, which we were wildly enthusiastic about, because you could put it in your backpack and carry it around, and it had all these wonderful fonts. So So anyway, I worked on site layout, I looked at the literature, I talked to people in industry to learn how we could do it better, I developed an interesting program, which of course, at the end had to be validated. And I remember the project manager from from Bechtel construction, who came and looked at my program kind of crunching away trying to figure out what laydown yard needed to go in which location and the first thing he basically said, Oh, Iris, can I grab the mouse and move things around. Which of course, totally violated this whole idea about we're going to automate this and take take it out of people's hands. So I realized we had work to do. But we also had work to do from from an academic sense, because, you know, in project management, we talk about managing resources and the resources that we manage our materials, manpower, and machines, and then of course, time and money. And lo and behold, I had spent years working on my PhD worrying about the resource space. And it dawned on me at the time that it was rather ironic that it wasn't even mentioned in the textbooks on project management, that space needed to be managed. Because the problem of managing space very much was delegated to people in the field. And and that's where all the decisions were made. So you know, I realized something was missing from the bigger picture in project management. I joined the faculty at the University of Michigan in Ann Arbor as an assistant professor actually, I was in the same cohort as Jeff liker, who joined the industrial engineering faculty and awards who joined mechanical engineering and there were several other faculty who came from from different places Bill Birmingham, one of my colleagues in electrical engineering, computer science, we're sort of all of the same cohort hired from various universities working on artificial intelligence problems and especially Jeff and I'll working on social technical systems. So So really understanding that we have this automation, but people are always wanting to, will always want to hold the mouse and try to do something different in case the computer doesn't do what they have in mind. So we were, we were kind of on the same wavelength.
As for my own interest, I branched out at Michigan from kind of the site layout problem into materials management, and then several years later into supply chain management really trying to understand the bigger the bigger picture problems. But what's interesting to know about about the timeline, is that around the same time, early 1990s, my colleague, Lauri Koskela, at the time was still in Finland, developed a technical report during a sabbatical at Stanford, where he looked at the literature very extensively and try to understand what the different frameworks were the people were using to develop models and optimize the problems that they had formulated. And he recognized three different kinds of bodies of knowledge. So one is the transformation for you in production, which is what we very much follow in traditional project management, it's transforming inputs into outputs, and trying to do that as fast as we can. But separately from transformation. There's also the flow view of production or queueing theory theory as it's called, in industrial engineering, the flow view of production that says, well, it's all well and good that you transform inputs to outputs. But if there's no customer for your outputs, your outputs are going to pile up, you're going to have a lot of inventory, a lot of stuff in between who knows that you're ever going to have a customer for it. So maybe you should also pay attention to these handoffs in between and not just on the transformation part. And then the third dimension, of course, is the value part, the value part, it says, Well, what good is transformation and what good is worrying about the in betweens buffers and the handoffs, if you're not creating something that's going to be of value to your customer. So interestingly, the these three views on production very much existed in the literature, but they seem to be disjointed bodies of knowledge. And Lauri's big contribution to our community was to say, you really want to do all three, right? You really you need to do transformation, to create something that the customer wants, but you want to do it with with nothing in stores, right? You want to do it fast, short cycle times, little inventory, and you want to produce something that's really of high quality that the customer is happy to pay for. So that was a big, aha moment. The other sort of independent evolution at the time was when dollars work. So Glenn Ballard, found had started off as a Pipe Fitter in the industrial engineering role and then moved out from from industrial facilities, industrial construction, moved into crew leadership, and then became a productivity improvement consultant over time. And he realized that many times, you know, as he was working as a pipe fitter, he was giving assignments that were just not doable, they didn't have the right instructions, they didn't have the right materials. They didn't have access to the right space to do the work, they didn't have the right tools. And so you know, he had kind of come to this, this synthesis that said, you know, if you if you're going to make assignments, you need to make sound assignments, you need to remove the constraints, you need to make sure that people know what it is they're going to do. You need to make sure that they have the resources and the capacity to do it so that the ideas of the last planner system kind of were germinating in the 1980s. And then, in 1994, Glenn wrote a paper on this first paper on the last planner system. So back to back to Michigan. So I was working on on socio technical systems and looking at the broader materials management aspects. As after six years there, I took a sabbatical, I realized that the literature wasn't going to help me enough to really understand what happens in industry. And I ended up on a large oil refinery project in Houston along the Pasadena shift channel. I had read the literature, I had read a CII report about materials management, CII, I had used a specific company HP Zackary as the exemplar of really good materials management system. And so I thought, if I'm gonna learn something I need to go learn from the best I don't I tried to get on a project with HP Zachary. And I was fortunate that their head of materials management, Jim Goodwin, allowed me to basically take take a chair, take a desk next to him on this this very large oil refinery project. I was there at the time. So this is '95 '96. I was there to help figure out with the newest technology barcodes, laser based positioning systems, tried to figure out how people manage their lead on yards and if there was a way to do We'd better with with automated systems. And obviously, all these technologies were in their infancy at the time. So there was a lot of testing a lot of trial and error to make it work. But it was, it was fun, I chased a lot of pipe and steel
tried to find in many different locations. So after that, I joined the faculty at at UC Berkeley. And I remember the summer before the semester started having lunch with Glenn and, and, and just telling him it's like Glenn, I don't quite understand this. As an academic, I didn't know much about materials management, I spend a year in the industry to find out from the very good company what the best practices are. And lo and behold, they have all this pipe and steel, and it's there in the Houston Sun sunning for for weeks for months. For the longest time, this is really not working very well, you know, I thought I would, I would have discovered the secret that we're far, far from having the secret. And so Glenn then explained to me, you know, what was happening in the industry kind of in a nutshell is in, you know, well, if you don't have a stable construction schedule, it's very hard to supply materials to match the construction schedule. But likewise, of course, if you have a lot of variability in your supply chains, it's really hard to supply even if your your construction schedule would be would be steady, right? It's hard to have a construction schedule if you have unreliable supply. So you know, we started this conversation about, you know, we need to we need to work as Glenn called it behind the shield, right stabilizing production at the construction site. And at the same time, we really need to manage that inflow of the different flows to the workspace to stabilize, right, we need to we need to attack variability.
Felipe Engineer 16:50
I think it's worth noting, Iris that, you know, when I started this journey of construction, so many years ago, we had cutting edge technology at the time when I started was a fax machine, and email was just coming online. And we were still getting RFIs by mail. And we're still getting RFIs by fax. And that was 20 ish plus years ago. And so, schedules were printed on large sheets, and they had to pull like a nail in the string down to see where you were in the current data date. And then they were filling in the prints by hand to show progress. But there is massive variability that it wasn't even time efficient to to print out these giant schedules took so much time that it wasn't effective, or cost efficient for projects to print these out with any kind of regularity back, you know that time ago, but and that's when it was simpler when 16 to 25 contracts could do, say a $70 million project. And now today, you're upwards of 120 contracts to do a project of the same dollar size. So you have more communication channels to manage more supply chain that's more specialized. And so you're introducing so much more complexity to project schedules. So the problem is getting with increased specialization, the problem is getting harder, unless you introduce a framework that limits work in progress or a pool system. Like we have in less plan or the Agile frameworks like Scrum or simple Kanban. So I think it's like, it's fascinating that all the things that you mentioned, were problems back in the 80s and 90s are still problems today, we have not solved those problems. And we don't have a magical cure. I think because you still you have so many people coming into the industry, people leaving the industry. And that knowledge transfer isn't one for one. Because of how people learned everybody today, Iris, I guarantee you still they're still grabbing the mouse, even if better practices exist or standards exist. So that's, it's fascinating to hear that that's still so problematic.
Iris 19:09
Yeah. I mean, let's not click the mouse too much right, in the sense that I think people need to buy into what they see on the computer, right? We don't want to be in control. We don't want to be this. My colleague, former colleague, Greg Howell would say we don't want to be the helpless victims of fate, right, we do. We do want to understand what the computers do that you know, at the same time, you know, we have all the power to to engineer the production system, right to structure the designs to structure the handoffs to structure the task so that we can, you know, create criteria reliability in the system. I you know, so many people say our industry is so complex, you know, and it's becoming increasingly complex. And, you know, my my thought has always been well, yes, our systems are complex, but Part of the complexity is what I would call self inflicted complexity. We make them complex, right? And then we make them complex and then we complain that the thing is complex, you know, the reality is you can simplify, you can try out some of the variability. So, I mean, back to this example on on the this project in Houston, you know, pipe spools are all one of a kind, right engineers like to engineer my colleague, John JIRA would have said Architects like to architect, you know, we'd like to generate value, right, we like to, I like to do unique things. But we have to think about whether creating everything to be unique is actually helping to create value, or whether it's going to kill us in the degree of complexity of recreating as a result. So I developed a fun computer simulation model, actually, with some data that Glenn Ballard and Greg had collected on a number of CI projects about the piping function and how people were managing the deliverable of, of design documents, isometrics, and how they were then managing the production of pipe spools and then delivering them to site, I use some data from that report, and created a discrete event simulation model. And the model specifically addressed this problem, what I call have matching components. So if every pipe spool is unique, and if every location on your oil refinery is unique as well, you have to match the product, just so. And if for some reason, you know, a piece is missing, you probably cannot complete the work on the assembly. Right. So all that said, you know, of course, if you can make things more substitutable than the matching problem is alleviated, then the complexity in your production system is produced, and it becomes much easier to manage. So I my computer simulation model has some very convincing, I think data to show that reducing product variability really helps with reducing process complexity in managing. It's, I mean, it's, of course, something we know. But we don't necessarily intentionally pursue that, that lesson learned, as we design and as we create our production systems.
Felipe Engineer 22:22
That's right. And I want to just, like remind everybody that I'm sitting here with a decade of experience in last planner system, and every project that I've had experienced deploying it on, has gained scheduled time and has either met or exceeded by exceeded I mean, did better than what the original schedulers have predicted. So, and that's even today, I mean, this recent is a week ago, it still it still delivers such a high reliability as compared to the alternative. It's just where if you if you just let things alone, and you think of that very linear approach, you're going to have undue complexity to use your language or just projects are going to take longer. And we do like to complain about why they take so long, that is actually true that you can there are our tools and things that we've learned from research that you've done with a lot of the people that you've mentioned, that has been transformational, into making project delivery, more reliable. I've experienced it firsthand.
Iris 23:22
Yeah, they're old ideas, but they work great. I think I use them every day. And, you know, I can highly encourage other people to use these practices as well. But it's hard to be it's hard to not introduce frivolous variability, right? Frivolous variability as in, oh, you know, I didn't think about it, I'll just go do something else. It's very hard for people to standardize and be very rigorous with their standards, people tend to be creative, and we want to go do some different things.
Felipe Engineer 23:57
Or we don't like, like Glenn had said before, we don't give people clear expectations of what needs to be done. And so they have to innovate on the fly, which is not always going to be more productive. If we let people step back and think about what they're going to do before they actually go forward to do it. We often just say, go get it done. And we don't say, think about it for 10 minutes, and then go do it.
Iris 24:20
Right. And the other thing we don't mention is to think about where were we all fit within the systems that we work in, right and, and that your performance can only be as good as the system's performance can be. I mean, if you work faster, but the bottleneck is somewhere else you're working faster isn't going to help,
Felipe Engineer 24:38
right? It's just gonna wear me out. I'm gonna get tired.
Iris 24:41
Exactly, exactly. Yeah. So that systems view is typically lacking and I think that's that's one of the perspective certainly that Lean Thinking is trying to advocate right it's about seeing the whole and, and as it as it talks about seeing the whole of course as you expand the problem To be more and more comprehensive, it becomes increasingly impossible to solve them from an optimization perspective, right. So you have to look at satisfying solutions. And you have to be clear as to what criteria you're going to use to determine what's satisfactory or not.
Felipe Engineer 25:15
Sometimes even thinking about constraints, some people see constraints only as negative. But there are such a thing as enabling constraints. I've read some of the work of Dave Snowden, and his complexity theory Cynefin. And he's talks about setting up constraints to enable things like scaffolding, just like we do in the scrum framework, or in last planner system with having five, five connected conversations in a certain sequence. When they're done in that sequence, you've created enabling constraints or scaffolding that allows for information to flow. And people have the opportunity to plan logistical flow, like you talked about, especially that the site setup that site setup is I think, something that is totally worth exploring, if you're on a construction project now. And your job is behind schedule, take a look at the flow of how your site is set up, you probably have a lot of excess inventory. And a lot of that is people just being protective, having some additional buffers, because there's more sporadic chaotic scheduling calls for materials and nobody wants to be caught not having things readily available.
Iris 26:24
Yeah. And people like to stick out turf, right, it tried to get ready and then block others from doing the work that they do. And then oftentimes back to the system thinking, right, we don't really understand where the constraint is. And so there may be resource constraints that could be alleviated. But we don't see them and everybody kind of suffers through them.
Felipe Engineer 26:43
You have internal pressures on every single company needing to hit their numbers. And those production numbers are not optimized for complete project throughput because they don't have the visibility of the full project needs.
Iris 26:56
That's right. That's right. They don't have the visibility, and they don't they don't have the information. Right. So. So you know, when I when I joined the faculty, obviously, at Berkeley, obviously, this discussion about last planner very much resonated with what I had seen of this large project in Houston. The other thing that I had the opportunity to get involved, as is Glenn Ballard, at the time, was working with Todd's Ebell. And Todd had a roofing company called Pacific contracting. And I remember hanging out with with Todd and Glenn on San Francisco Airport board, boarding areas a and g, as thought was putting in new roofing work. And Todd, you know, had very much understood that, you know, as a contractor, they were oftentimes lacking information and lacking specifications on the methods that they needed to use to, you know, apply multiple layers. And of course, if you're a roofing contractor, it really matters that you do good work, because if there's a leak in the building, it's your fault. And so Todd had moved into modeling things in great detail, right in AutoCAD, and then the later on in three dimensional representations 3d to to define the design, from this more general Architectural Description all the way down to step by step, procedure specifications specification for what is the worker going to do on site? And so that, that greatly helped in completing the picture as to, you know, what are we expecting workers to do.
Felipe Engineer 28:30
Yeah, for people that don't know, roofing drawings in architectural plans require a lot of math in order to fully understand what's going on just the nature of how it's depicted in two dimensions, with the slope, and it doesn't always calculate out as designed because of, of nuances and little changes and tolerances that can add up. So I think that's it's worthwhile to model it and find all the special points.
Iris 28:59
And it's, I mean, it's still you mentioned tolerances is one of my, my favorite topics to talk about, too, you know, you mentioned tolerances, so So oftentimes, when we develop our computer models, they're building information models is very little indication about the fact that there are tolerances, right, the fact that there will be dimensional variation that you you know, as Todd said, you know, the buildings leak at the intersection of contracts.
You know, it's true, right? It's you have to, you have to understand that different trades work to different tolerance requirements. And, you know, what the American Concrete Institute specifies isn't necessarily in line with what the Institute of steel construction specifies. And so, you know, up until relatively recently, actually, the standard for example, for anchor bolts in concrete were not in alignment. And so you start off with a problem right because every trade It builds to their industries, tolerance, expectations and standards. And if from the get go, they're not aligned with one another, you're going to have problems.
Felipe Engineer 30:11
Somebody has to compromise. If they're in conflict, and who's going to give, then you got to have the authorities having jurisdiction have to weigh in. Mm hmm. So it depends on who you get. There's more variability and how that's gonna get resolved.
Iris 30:26
That's right. That's right. And if you're the last the last kid on the block, the last one to do the work, then you need to get out the grinder, right, or you need to get out the caulking to fill the gaps. Right part of our standard practices.
Felipe Engineer 30:42
That's right. Just laughing because that's happened more times than I can count on a project where we've got all this additional scope for caulking or remedial work just to put contract work in place, because it just, it's all within contract, but it doesn't fit doesn't work.
Iris 31:02
So this is what I mean, with production system design, right? If we begin to understand what the problems are, certainly we can we can try to alleviate them, right, try to design our systems such that these problems are much less likely to occur. So we don't have to get the grinders up, right back to the system's thinking in the early. Well, actually, it also in the 1990s. In California, there was a Senate Bill 1953, that basically created a crisis in the industry. And again, one of our sayings, you know, it's, you know, never let a good crisis go to waste. The crisis that was created with with the Senate bill, and with the associated Government Association called OSHPD, the Office of Statewide Health Planning and Development was that the state of California wanted to have whole large hospital owners, who had acute care facilities, ascertained that their acute care facilities would not only remain standing after a major earthquake, but also remain fully functional. And on top of that, the owners were mandated to either upgrade their facilities or to demolish and rebuild, to the to that new standard within, you know, very strict time limits, which basically led all the owners to begin to think about how can we actually get enough attention of the architects and of the engineers and of the builders in our industry? Who do health care construction? How can we? How do we get their attention, so we have the capacity to actually comply with the state's regulatory requirements. Among all the different owners was Sutter Health, a large organization in Northern California, but in the state of California, certainly not the largest health care provider was one of the players, thinking about the fact that because there was going to be such tremendous demand on architects and engineers and builders to upgrade these facilities that they might be, they might not find the best companies to work with. And the big aha moment that they had was to think maybe there is a different way in which we can interact with our design and construction community, maybe there's a way that we can become the owners of choice, so that we don't have to go beg these companies to work for us. But conversely, they will come to us because they want to work for us. And so lean, lean became kind of the big, aha moment for Sutter Health. They said, let's figure out how we can become lean owners how we can deliver our facilities in the Lean fashion. And so they challenged the construction industry to to adopt lean practices. As part of the the, the transformation that they were after they actually made it mandatory for every construction company and every design firm that worked for them to have a lien coordinator and all the lien coordinators across their project had to have dinner once a month to talk to one another and share the lessons learned at the beginning. Sutter Health would very generously pay for dinner and then of course, the attendance grew and people like myself began to attend as well. And then the baton was passed to different companies to pay the bill as well. But it was really a brilliant a brilliant move to bring the community together. And I remember I was actually present at the dinner where, you know, different architects, different engineers, different contractors were complaining about how awful OSHPD was right OSHPD is kind of has been a really, really bad word. And I remember
I believe it was Carl Sherman, from Sutter Health kind of standing up and saying Well, isn't this a little bit ironic? You know, we talk about working together as a team. And here we are, you know, designers, engineers, builders with the owner, we have everybody in the room, except OSHPD. Why is OSHPD not here, and he stepped out and invited OSHPD to come to the dinners. So we could talk about the problems that we had. And the problems of course, generally speaking, being the problems of our industry, right, there was a lot of finger pointing at OSHPD, but it was really the problem of the industry. And John Gillen Garten, who was the deputy head of OSHPD came to the dinner, and basically said, Listen, you know, I know, I know that Josh Powell is taking a long time to do the review. But you know, we have staffing challenges. And these reviews are just incredibly complex, because you need to look at the entire system perspective, right after an earthquake is your building going to remain fully operational, there are many systems that need to interact, this is really complex. It was very difficult. Of course, once people had developed a lot of competence in that area, the private industry would hide him away, and so washboard could start all over again, with training, training personnel. So as a real challenge, that I remember an architect in the room, kind of being rather angry and sort of commenting. It's like, well, but why, you know, when I when I send in my drawings for review to OSHPD, right? Why does it take six months for you to review them? And then get back to me and basically say, well, you're missing this and this and this piece of information, right? Couldn't you have looked earlier? Couldn't you have commented on that earlier? Why do you have to wait six months, and then the room got very quiet, and the room got very quiet? Because everybody began to think, why should we blame OSHPD for that? Right? If you submit drawings that are incomplete, you created the problem. Don't blame OSHPD for it.
So there was a turning moment in the industry. So we took the challenge polarizer from bolt Glenn, and myself kind of took the challenge and said, Well, what we really need is bring the industry together, right? There's Sutter Health. But of course, all the healthcare providers have the same problem. And there's a lot of companies that work for Sutter, but the number of other companies that work across the industry, let's actually figure out what it is that autopot once. And that was basically the start of what we call our project production systems lab at UC Berkeley. So in 2005, with the sponsorship from volte and other companies, we actually launched a number of planning meetings, where we developed value stream maps, the value stream map to design and deliver the handoff to ashphalt for 100 bed hospital. We were set up in four different rooms in Fairfield. Every room had an arthropod representative and then we broke up the other participants to to build more or less equal teams. And then we dug in and we began to develop a current state value stream map for how you deliver 100 bed hospital. And then over the course of four weeks, we actually dealt to a future state value stream map as well. So that's birth, you know, a wonderful conversation in the industry where people began to realize that, you know, if OSHPD if we submit incomplete drawings to ash fall dashpot is going to get back to us we'll have a back check. Right? If we try to shorten the cycle by submitting our drawings even earlier, our drawings are going to be even more incomplete. And so there will be not one but perhaps several back check cycles, right? The system was spiraling all the way down and just getting worse and worse with review cycles taking way too long. And so with that, that PSL planning exercise kind of a neutral ground, right, we were able to, to help foster that conversation in the industry to talk about understanding the system and understanding the multitude of different customers in the system and understanding that, you know, your first customer of design obviously is the regulatory agency. And of course, you know, construction comes in of course the owner comes after hurts, but there are a multitude of of customers and we need to tailor our deliverables to meet the requirements of these customers. We documented a nice case you know, with Sutter hills, where they actually changed the way they were coloring up their building information model to make smoke compartments for example, very visible to really cater to the fast Aashirvaad review and then all kinds of other practices stemmed from that so Ashfall didn't necessarily have the latest building information modeling technology, but the design team could actually lend a person with a computer to On the latest information technology, squares sitting next to an arch bot person to help with a review, for example, so that Ash but wouldn't have, you know, a pile of 1000s of drawings to go through. So there's a lot of a lot of good ideas were implemented as a result of that. And that launched that launched our project production systems lab. So we have been kind of a neutral ground for industry where people can come together, they can take their project hats off, they don't have to be defending their title or their position or their claims on any one project. And we've been very encouraging to have, you know, good, good conversations and really tackle industry challenges.
Felipe Engineer 40:41
Yeah, P2SL, someplace, I got to visit UC Berkeley myself some years ago. And that's where I learned about takt planning, which at that time was introduced as the sixth conversation inside of last planner system to get an even more reliable schedule, using different techniques like line of balance, and Location Based Scheduling. And it, it colored and changed my approach to life planner system ever since it got much better. And I've recently taken a trip abroad to visit my counterpart at BMW in Bavaria, in Germany, in Munich, and gotten to see what they've been able to accomplish with tack time on construction projects, not automobile lines. And it is incredible to see the reductions in scheduled time. And again, it's like having that focus on the planning cycle, designing your production system. And the crazy thing is, it doesn't take a lot of time to set it up. It's very fast. And that I would say that the learning curve to even deploy it is an investment of maybe a couple of days, and then a day or two of noodling. And then you can bring your trade partners in review a draft schedule, that's far less complex than 100 Plus page 1000, activity critical path method schedule. And so that came from research. And I, we were talking the other day, and I asked you, how many years have you been studying takt and research.
Iris 42:13
So I was fortunate again, to, to learn about takt from from a project, the Women's and Children's Hospital in Sacramento were bolts, was trying to gain time on their schedule and building the exterior works. And so I think, again, necessity is the mother of invention. They thought they really needed to try something different than exploring multitude of different options. And so they ended up using takt with with amazing results. I don't have the chance, I went back to Sutter here in the Bay Area. And I asked for some projects that, you know, we had like to study with with my students in class and with our research and James Spees responded with one project, although it was a little bit too far long at the time for us to do any kind of intervention, any kind of experiments. But then another project came along the mills hospital, and the mills Peninsula Hospital and the project team was just just kind of deciding what kind of lean practices they were going to use on their project. And James piece introduced, my students and me to the project team talked about tax what we wanted to try and do you know the project team bought on. And so we use takt and as a way to structure the face schedule. And then we use takt of course in execution of the project. I wouldn't call that first experiment. Truly tax planning it was it was a complex it was small but but the router complex get and remodel project. So in a traditional sense of tax planning, tax planning is often used in in, like hospitals where you have many rooms that are the same or hotels or ship building, we have many components that are physically the same or very similar. The project that we looked at, didn't have that much similarity from a from an architectural perspective from a product component perspective. But I realized that the time that product component, repetition didn't really matter. Because we have skilled craftspeople and they have a multitude of skills, they can do many different tasks. So I came through that experiment to the realization that we really needed to focus on what's called work what I called Work density. And work density is you know, for a given area on a given Scope of Work with your crews means and methods, you know, prefabrication strategy, whatever you have in mind, how much time are you going to spend in that specific area? And if we can capture that for all the different trades, right, we can begin to balance those times right I call these these times workloads or work densities we can begin to play with these numbers we can change The zoning of the site to even out the workloads across the different trades. And we can also begin to think about trade offs. Right? If I invest a little bit more maybe to prefabricated components somewhere else, perhaps it costs more, maybe not. But perhaps it costs more to prefabricate. If I can prefabricate, if I make that investment, and it can lower the work density on site, I may be able to actually get everybody to work faster in a, you know, a faster takt in a shorter cycle time on the project itself. So through work density, we can have some some really useful conversations about system design,
Felipe Engineer 45:39
That through that work density, it doesn't mean that the workers have to perform quicker or harder, it just, it actually allows them to perform at an even pace. And this is what I got to learn in Germany with the the metaphor of the trains, and the tank wagons the same exact thing as your calling the density, we just set the the wagon size to a certain size, maybe your wagon is this big, maybe it's this big, depending on the the crew mix, maybe one wagon has a single crew, and another wagon have a different production values might require two or three crews to balance in size to the one curve. So you get the uniform wagon size, and then you create this magical throughput. That's just incredible to see. And so I recommend, I mean, there's videos online to see tax simulations on YouTube. So people go out there, check that out or read the idlc papers. And I just recently had somebody on the show, Iris Pete, I believe was the project manager of that Sutter project where they started using takt on the exterior. And he said that his superintendent was just so determined. I think his name was Dan Murphy. Does that sound familiar? Yes, yes. Yeah, he said Dan Murphy was so determined that he was going to make it work that he tried something like 11 times, and it failed, before it worked. And then when it worked, it was like magic.
Iris 47:02
And he knows and he you know, as a superintendent, I mean, sort of, regardless of what the owner requires, you know, regardless of other scheduling systems that you know, are contractually mandated or preferred, you know, he will take his job, right, you know, it makes it makes such good sense to have these smaller chunks of work, to have to have smaller zones, to be much more clear about the handoffs, right, to have rapid feedback, you know, if you have a two day tacked in zone, after one day, you already know whether it's quite likely or not that you're going to finish in day two and day two, you know, what are you finished or not, you can immediately respond to any corrections that are needed. There's sort of this economy of multiples, right, that that really begins to play to your advantage. And it does wonders, as you say, it goes one. I think there's a lot, there's a lot still to be learned on tax planning. And as you know, from from colleagues in other country, also colleagues in the United States on, you know, different people in industry than Murphy and others who are using tax planning. There are many, many different ways in which people are using tax planning, of course, because the context of the projects in which they work are different than the trade partners involved, of course, have made your input and how the tax plan can be developed and unfolds. So I think there's, there's, there's so much more to learn about that. Very excited about, about the prospect of documenting more cases and running more experiments.
Felipe Engineer 48:40
Oh, we're definitely going to, we are definitely going to this is the this is what Pete said from his perspective is the new wave of what's going to sweep across the industry and really accelerate lean adoption. Because it is just, it's just so much better for it handles the the worker crisis of the shortage, and handles a lot of the safety issues where people don't have to work at abnormal paces. The reliability is so much higher, the clients love it because they get much more reliability on the plan. And they can focus the transition into the buildings or the structures, much more reliability. I mean, everybody wins. And the people that do it like the trade partners, they are much more profitable because the the constraints are being removed. And the work that they're able to do is much higher quality. I've heard from the our partners overseas in Europe, the punch lists are completely eliminated, or minimized to very minor things to almost nothing, which is like incredible, like that's one of the things that robs people of like financial and employee morale, when they they do defective work because the system is forcing them to.
Iris 50:02
Right or the frustration that they have. Because as I mentioned, you know, Glenn Ballard early experiences before the last planner is, you know, you want to do good work, but you don't have the right instructions. And so you have to kind of make it up on the fly and do something. And then it turns out, it's wrong. But you don't have the material and you have to put something you put a temporary structure in, and then you have to come back later to fix it, you know, to do it, right. I mean, that's all frustration. That's really not not good.
Felipe Engineer 50:30
Right? What do you see from your perspective? For people that think Lean is too academic? In other words, they believe it's something that's lectured about, but it doesn't work in the real world? What would you say to those people,
Iris 50:41
There's a famous thing, that's nothing quite as practical as a good theory. You know, there's, there's a, there's a lot of a lot of science, there's a lot of, you know, there is a field called production science. So there's a lot of science that's available to be used if people want to use it. So in that sense, certainly, I would highly encourage people to read the academic papers from, you know, the International Group for Lean construction, and, and so many other places. You know, at the same time, you know, theories need to be tested, right, they need to be grounded in practice. I think Taiichi Ohno when he developed over, you know, 3040 years at Toyota, the Toyota Production System, I think, that was all grounded in good practical application, but not just application, I think what came with the application was a systematic approach, right? The Plan, Do Check Act of continuous improvement. So, it's repeated execution to make sure that you have process capability that you can reliably execute that you have predictable outcomes. So you can standardize your processes, and you know, what the output is going to be. And then once you standardize your processes, then you can do experiments by changing your processes and, and, you know, try to to find improvements to it. Right. So but that's a very systematic process that gets applied in practice, if people if people want to become good learners, lien has a lot, a lot to offer
Felipe Engineer 52:15
in that regard. Absolutely. And I see and I've said it before, and I'll say it again, from my perspective of studying this for over a decade. lien is a synonym with learning, when you get really deep into it. It's that learners mindset. That is the what I argue is the natural state of human beings, highly adaptive creatures that we are. That's what we need to encourage you to have more often I just saw yesterday on Twitter at nine o'clock at night, my time in California, which was I think it was like it was Sunday, Mike Rother tweeted Mike Rother famously developed the Toyota improvement kata, he tweeted a paper from aglc, published in I think it was Peru, researchers working on a construction project site using the Toyota improvement kata to get the complete last planner system implemented, and show that it happened with success very fast, much more rapidly versus the traditional ways that last winter is deployed. So I just thought, like, what fitting that I'm seeing a tweet from Mike and Mike studied it in Michigan to what school
Iris 53:27
He was in industrial engineering, right. I mean, he worked with Jeff Liker, they had a big automotive manufacturing program in the early 1990s.
Felipe Engineer 53:35
So another a lot of magical things happening all over the United States and academia helping projects even to this day,
Iris 53:42
The academic world, the academics, I think, are the providers of the new generation of people entering our industry, you know, engage a gauge academics on your projects. And, you know, let's, let's learn together, let's use these bright minds, the openness that our students have to explore better ways of working.
Felipe Engineer 54:04
It's been a pleasure and a treat, and I'm ready and excited and engaged to go learn some more.
Iris 54:09
Thanks for having me. It's a pleasure.
Felipe Engineer 54:12
Very special thanks to my guest. I'm Felipe Engineer-Manriquez. The EBFC Show is created by Felipe and produced by a passion to build easier and better. Thanks for listening. Stay safe everybody. Let's go build!